Environmental Report 2014
Zero Emissions
The JAE Group makes effective use of resources by reducing general waste by consuming less paper, while promoting recycling and sale of valuable resources through the exhaustive sorting of waste, such as scrap plastic and metal.Zero Emissions Activities
After launching its zero emissions efforts in fiscal 2000, JAE achieved a recycling rate of 99% in fiscal 2004, and kept it at the 99% level thereafter.
Thanks to the JAE Group’s efforts to promote the sale of plastic and metal waste, the sales rate of all valuable resources has exceeded 60% since fiscal 2006. In addition to reducing costs for waste treatment, the sale of valuable waste contributes to resource saving and the reduction of CO2 over the life cycle of products. The Group aims to achieve even higher rates of sales.
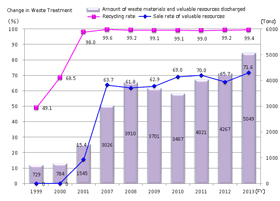
Change in Waste Treatment
Note: The JAE Group defines zero emissions as achieving a recycling rate of 99% or higher for waste defined by local ordinances, excluding waste that is disposed of by incineration and simple landfills.
Efforts for Proper Disposal of Waste Materials
The JAE Group is implementing proper disposal of waste materials in accordance with Japan's Waste Disposal Law. The Group conducts compliance studies on subcontractors that handle all types of industrial waste, general waste, and valuable resources at the time of contract signing and periodically thereafter by periodically checking their licenses and performing on-site inspections.
To increase the transparency of its industrial waste disposal, in fiscal 2011 JAE began to electronically maintain industrial waste manifests, and in fiscal 2013, all new industrial waste manifests were stored exclusively in electronic form. Since fiscal 2012, JAE has been working to develop this initiative across the entire Group, and in fiscal 2013, it was able to achieve electronic manifest operations for 100% of participating suppliers. JAE continues to strive to properly process waste materials.
Main Activities in FY 2013
The main efforts made by sites to reduce wastes are shown below.•Promotion of waste plastic recycling (JAE, HAE)
With regard to processing waste materials, actions are taken with a view to environmental considerations (Scope 3), JAE and HAE selected recycling vendors, and cutting costs of waste processing by changing disposal methods and contributed to lower CO2 emissions.
• Promotion of waste glass recycling (JAE)
Since fiscal 2013, increased production of touch panels has led to a higher volume of waste glass. By taking such actions as making adjustments together with recycling vendors, JAE contributed to higher recycling quality.
• Advancing the proper disposal of polychlorinated biphenyl
In fiscal 2013 the Group was able to conduct the disposal of a portion of its polychlorinated biphenyl. The Group continues to properly work at its disposal activities.
• Promoting the recovery of valuable waste plastics (HAE, YAE)
The JAE Group is striving to improve the sales rate of waste plastics by thoroughly sorting them during recovery, promoting reuse within the company, liaising with recycling firms, and other measures.
• Promoting the recovery of valuable waste metals (HAE, YAE, SAE)
Exhaustive efforts to sort and recover waste metals contribute to efficient resource utilization and are helping to improve the rate of valuable waste that can be sold.
• Recovery of Ni from plating sludge (HAE)
In fiscal 2011, the company began recovering Ni from plating sludge, contributing to cost reduction through the double effect of reducing waste processing expenses and sale of the resource.
• Recycling cleaning fluids (YAE)
To promote the recycling of cleaning fluids, the company completely separated the recovery of waste oil and waste fluids and redefined them as saleable substances, rather than waste, reducing waste to zero.
• Reducing waste by lowering process defects (HAE, YAE, SAE)
The company is cutting waste by reducing the rate of defects, setting targets for the process defect rate and so on. The defect rate was reduced in line with the target by improving quality and workability through measures such as upgrading tools and procedures, reinforcing component target value management, and enhancing the skills of workers. This resulted in commensurate waste reductions.
Letters in parentheses, such as JAE, are abbreviations of the sites that carried out the activities.
The company will continue its efforts toward eradicating defects and promoting manufacturing that is environmentally friendly.