Environmental Report 2011
Green Procurement
In order to establish an environmental protection system across the entire supply chain, Green Procurement Guidelines, which serve as the common standard for the whole JAE Group, are provided to business partners. These guidelines ask suppliers and other partners to build environmental management systems, manage substances that have an environmental impact by regulating their use in manufacturing processes, and ban, avoid, or manage their use in products. In this manner, the JAE Group and its partners implement integrated hazardous chemical substance management.In addition, environmental quality checks are carried out periodically for all partners to verify the implementation status of the aforementioned efforts, and environmental quality is also being checked for the suppliers serving those business partners, and so on up the line when processes thought to be particularly crucial are involved.
An environmental management plan is formulated each fiscal year for checking environmental quality, and progress is managed. The results of the FY 2010 environmental management plan are as shown hereafter. Results surpassing target values were achieved.
Number of business partners for which FY 2010 environmental quality checks were implemented: 224 companies (target value was 196 companies)
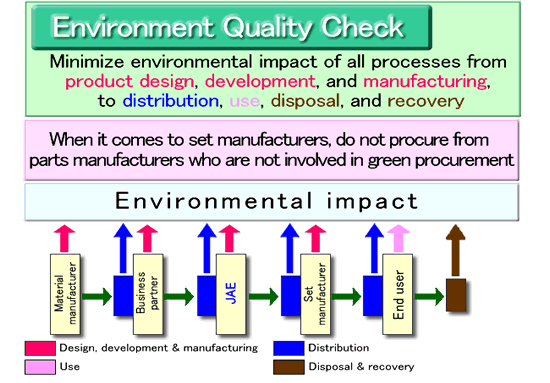
Certification of Environmental Advisors
In FY 2004, the JAE Group introduced a certification system for Environmental Advisors responsible for checking the environmental quality at suppliers. Under this system, only people who undergo the necessary training and pass a test receive certification. In FY 2010, 47 new Environmental Advisors were certified in Japan and overseas. As a result, some 300 of these advisors were actively checking environmental quality at suppliers in Japan and overseas as of the end of March 2011.Management of Chemical Substance Content in Products
Newly developed products, such as connectors, are managed in a proprietary environmental database after obtaining certificates and analysis data for them in order to check environmental compliance and apply it to designs. In addition, x-ray fluorescence spectrometers are being installed at plants in Japan and overseas to analyze hazardous substances in incoming audits, initial product audits, and other audits, thereby building a management system that does not intake or output environmentally problematic products.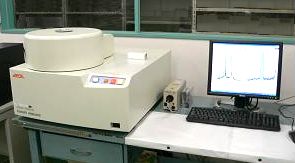
Furthermore, in order to check the status of the building of the environmental quality management system, efforts have been made to conduct internal environmental quality audits each year starting from 2006 and to maintain and enhance the system. In the FY 2010 audit, it was confirmed that both the system for environmental quality and its operation were well established.
Moving forward, the JAE Group will work hard to conduct audits that are even more rigorous and to upgrade its systems in an effort to make further improvements.
Communication with Business Partners
Building systems with business partners that are based on long-term trust is crucial to improving environmental quality. In FY 2010, we held a New Year's Party as a communication opportunity aimed at building relationships that mutually strengthen ties with our business partners. We also worked to forge strong partnerships by holding a Procurement Policy Orientation for our main business partners.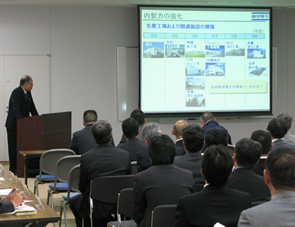