Environmental Report 2016
Reducing Environmental Risks
Addressing the Fluorocarbons Act
Japan's Fluorocarbons Recovery and Destruction Law was intended to secure the recovery and destruction of fluorocarbons associated with designated products. Upon its revision, the law's name was also changed to the "Act on Rational Use and Proper Management of Fluorocarbons." The revised Act went into force on April 1, 2015.Under the revised Act, controllers of Type-1 designated products are obligated to inspect relevant equipment and to keep records. They also must ascertain the amount of leakage, calculated from the recovery and loading volume of fluorocarbons in the course of maintenance or other operations. In the event the result of CO2 volume calculated is above a fixed amount, they are required to report to that effect.
The JAE Group operates in accordance with the revised Act, in line with the set process of understanding all of the equipment used, conducting inspections, recording, aggregating amount of calculated leakage and other tasks.
Throughout the JAE Group, there are some 1,400 pieces of equipment covered. In addition to general air conditioning and refrigeration units, there are oil coolers for production equipment and others, as well as thermostatic and humidifying chamber, and other testing equipment used to assess products, and other equipment.
In fiscal 2015, being the first year of the revised Act, each quarter JAE confirmed the status of each site, gave all relevant equipment simple inspections, and completed regularly scheduled inspections. It also confirmed that fluorocarbon manifests were properly maintained for equipment to be discarded.
The amount of calculated leakage occurring in the course of maintenance, repair and other work amounted to 177 tons (calculation of CO2 volume).
All equipment that uses fluorocarbons is subject to inspection, and as such, together with countermeasures to global warming caused by fluorocarbons leakage, JAE's response is also linked to the early detection of diminished energy efficiency caused by abnormalities or breakdowns in equipment.
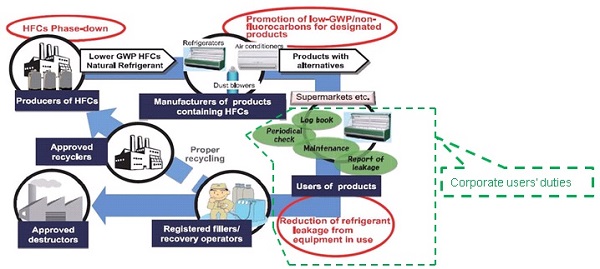
Prevention of Soil and Groundwater Pollution
The discovery of soil and groundwater contaminated with hazardous substances is on the rise in Japan due to the redevelopment of former plant sites and voluntary surveys. Since countermeasures after contamination has already occurred take a vast amount of time and money, this is gaining recognition every year as a massive social problem, and related laws and regulations are being put in place.The JAE Group conducts risk assessments of its facilities that handle toxic substances and those associated with fuel oil, and takes countermeasures to prevent contamination, such as by double-walling underground storage facilities and pipes. This section introduces several activities to prevent contamination.
2010: | JAE assessed risk of leakage and seepage into the soil with regard to its facilities that handle toxic substances and fuel oil-related facilities, then began to raise its underground pipes, installing them above ground (Japan Aviation Electronics Industry, Ltd., Akishima Plant) |
2013: | The JAE Group commenced inspections with regard to the aging and useful lifespan of environment-related equipment and at facilities designated for storage of toxic substances, and regularly replaces the main valves on collateral pipes and other parts at proper intervals so as to reduce the risk of leakage. (Japan Aviation Electronics Industry, Ltd., Akishima Plant) |
2014: | The above-ground installation of pipes, that had run underground, for toxic substances and those related to fuel oil, which had been assessed as high risk, was completed. Accompanying equipment upgrades to clean emissions generated in the plating process, the wastewater cleaning process tower's retainer walls were recoated. (JAE Hirosaki, Ltd.) |
2015: | In order to construct the Comprehensive Assessment and Testing Building, the former plant was demolished. Soil testing confirmed that there was no contamination. (Japan Aviation Electronics Industry, Ltd., Akishima Plant, former site of No. 4 plant) |