2023/10/31
-
Input/Output (IO) Connectors
JAE and Xenoma Collaborate on Smart Textile Connector Development
Japanese apparel startup Xenoma Inc. got its start from the confines of the University of Tokyo. Presently, it develops a wide range of products, particularly, embedded wearable sensor devices. Part of the company's development efforts include suits that make use of electric muscle stimulation that not only strengthens muscles but also increases their motion effects. JAE is working with Xenoma to develop connectors for commercialization.
In this article, Mr. Masao Nakajima, co-founder and CPO at Xenoma, and Mr. Akihiro Matsunaga of JAE's Connector Division, discussed the initiatives and outlook in developing the product.
Formidable Partnership
Matsunaga: JAE and Xenoma solidified a partnership during a tradeshow both companies attended. Smart apparel made of conductive-fiber-based textiles realizes high sensing levels that would be difficult to achieve in smartwatches. We reckon that in the future, the market for these products will further expand, especially in the area of preventive healthcare. Our efforts toward smart textiles began around 2016. Although we had known Xenoma through mass media, our encounter at your exhibition booth paved the way for our collaboration.
Akihiro Matsunaga, Product Development,
Connector Division, JAE
Mr. Masao Nakajima, Co-Founder & CPO,
Xenoma Inc.
Nakajima: Xenoma has been developing smart apparel that uses stretchable wiring, developed at the University of Tokyo, and has considered commercializing suits capable of generating electrical stimuli. However, this requires a high level of connection reliability with the stretchable wiring to ensure a safe and stable operation. Furthermore, we needed reliable connectors that would withstand extreme conditions such as washing machines. As electricity runs through these connectors, accidents must be completely avoided. What’s more, because it was difficult to produce them in-house, we believe JAE is the most suitable partner we can have.
Speed and Constant Planning
Matsunaga: Although our connectors had earned a good reputation among our customers, we had yet to mass-produce washable connectors. In addition, Xenoma approached us in the spring of 2019 with the goal to complete the development and begin selling the product by the end of the year. The JAE team was amazed by the speed with which Xenoma required us to develop a new connector.
Nakajima: Because I have worked with a large corporation before founding the start-up, I understand that time is needed in product development. Nonetheless, I was grateful for JAE’s quick response. Washing the smart apparel will not only expose the connector to forces of a washing machine, but also to strong agents such as detergent soap, flocs, and other undesirable elements. Xenoma asked JAE to develop a connector that meets the extreme scenarios of usage and resist deterioration.
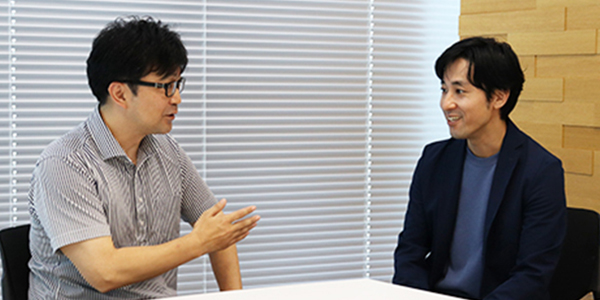
Matsunaga: Teams from Xenoma and JAE were meeting regularly and discussing ways to improve the connector. As the connector was to be assembled by workers on the production line of an apparel factory, it had to be product that they could easily assemble. JAE repeated trial production and invited members of Xenoma’s team to the test production line for possible suggestions in the assembly process. Moreover, to circumvent the long lead time required to make molds for custom-made plastic components, JAE adjusted specifications while producing machined prototype samples and assessing them together.
Nakajima: There have been thorough meetings, mostly every week. JAE formed a dedicated team for this project. That team racked their brain about structure and other features in various ways.