Environmental Report 2012
Green Procurement
Activities in FY 2011 (Result of activities)
In Europe, China, North America and the rest of the world, the requirements concerning the chemical constituents of products are becoming increasingly strict. There were no major revisions of the European RoHS regulations in FY 2011, but there were indications of additions to the regulated substances and additions to the CE mark regulations. However 27 substances have been added to the list of substances of very high concern (SVHC) in the European REACH regulations. In addition, the 2nd step of the Chinese RoHS is expected to be implemented shortly.In response to this situation, the JAE Group provides its business partners with Green Procurement Guidelines and maintains an environmental protection system across the entire supply chain for the management of chemical constituents. The cooperation of our business partners is also essential in eliminating these prohibited substances from products. Therefore, in principle, we carry out periodic environmental quality checks at all of our business partners every year with their cooperation.Additionally, the same kind of environmental quality checks are also conducted at lower-tier suppliers, especially when processes thought to be particularly crucial are involved.
These environmental quality checks are regarded as an important item within the environmental management system, and every FY year an environmental management plan is established and progress of the plan is monitored.Results surpassing the target values were achieved. The results of the FY 2011 environmental management plan were as follows.
Number of business partners for which FY 2011 environmental quality checks were implemented: 294 companies (target was 284 companies)
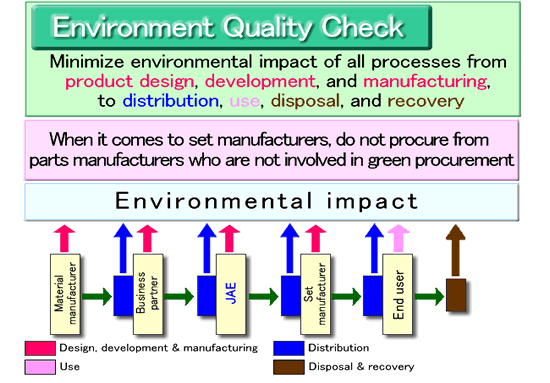
Certification of Environmental Advisors
In FY 2004, the JAE Group introduced a certification system for Environmental Advisors responsible for checking the environmental quality at suppliers.
Under this system, only people who undergo the necessary training and pass a test receive certification. In FY 2011, 35 new Environmental Advisors were certified in Japan and overseas.
There is a term of office for environmental advisers, and to renew their status, they must take a specific course of education and pass a test. In FY 2011, 73 people in Japan and overseas renewed successfully.As a result, some 320 of these advisors were actively checking environmental quality at suppliers in Japan and overseas as of the end of March 2012.
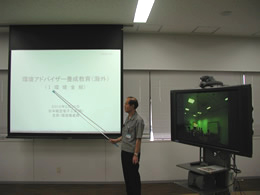
Establishment of an environmental quality control system
The JAE Group analyses the raw materials and components it purchases with X-ray fluorescence spectrometers as part of the acceptance inspection to check that there are no discrepancies between the chemical constituent data received from the supplier, and in the case of product shipments, that there are no discrepancies with the design data.These X-ray fluorescence spectrometers are being installed at plants in Japan and overseas, thereby building a management system that does not intake or output environmentally problematic products.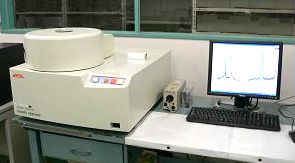
In addition, chemical constituent data is saved in a proprietary environmental database, allowing the company to respond to requests from customers for information on hazardous chemical constituents.
In order to check the progress in establishing the environmental quality management system, the company has conducted internal audits each year starting from 2006 and is working to enhance the system.
Communication with Business Partners
Building systems with business partners that are based on long-term trust is crucial to improving environmental quality.In FY 2011, we held a New Year's Party as a communication opportunity aimed at building relationships that mutually strengthen ties with our business partners.We also worked to forge strong partnerships by holding a Procurement Policy Orientation for our main business partners.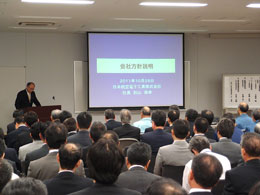