Environmental Report 2017
Measures against Climate Change
The fight against climate change is a crucial global issue that requires the further involvement of each and every person and organization.The JAE Group is working to address climate change through the teaching of environmental awareness, production-related measures, and measures at plant facilities, and it has set definite objectives and targets for its environmental activities.
Amount of CO2 emitted by the JAE Group in Japan
The total CO2 emissions of the JAE Group for fiscal 2016 amounted to 104,624 tons, an increase over the previous fiscal year. The main factor behind the increase of greenhouse gas emissions in the past five years was higher production. The improvement in emissions per unit of net sales in fiscal 2016 was due to efficient production.CO2 emissions volume by energy usage
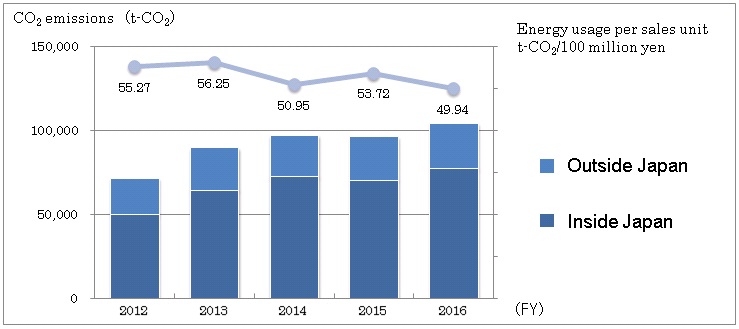
*Energy usage per sales unit is shown as unit of CO2 emissions in Japan and overseas, and consolidated net sales (unit: t-CO2/100 million yen)
*The equivalency factor for CO2 emissions due to energy use is the value published by the Federation of Electric Power Companies. In fiscal 2016, the fiscal 2015 result (0.531 tons-CO2/MWh) is being used.
Status of progress toward uniform goals in the electrical and electronics industries
The JAE Group in Japan participates in the electrical and electronics industries’ Action Plan for Achieving a Low Carbon Society and is progressing toward the goal of a 1% annual average improvement on a per-unit of energy basis through 2020.Although total energy usage is increasing in line with higher production volumes, we have curbed Although total energy usage is increasing in line with higher production volumes, we have curbed (use cursor to view definition) by taking steps at all sites to contribute to the fight against climate change.
In fiscal 2016, the improvement rate was 26.62% on a per-unit of energy basis, surpassing the goal of 3.94%.
Status of Response to Tokyo Cap-and-Trade Program
The Akishima Plant has an obligation to cut greenhouse gas emissions by an average of 15% during the second phase of the plan from fiscal 2015 to fiscal 2019.However, emissions in fiscal 2016 declined by about 11.2% from the baseline standard, and thus failed to reach a 15% reduction in a single fiscal year. The reason for the increase in greenhouse gas emissions was the expansion of production facilities, the operation of the Comprehensive Assessment and Testing Building, and other factors. We will keep working to do our part in the fight against climate change.
Fiscal 2016 Energy Conservation Case Studies
Case Study: Energy Conservation in Production● Attachment of insulation covers to molding machine cylinders
We are systematically working on insulation at HAE and YAE. At HAE, we achieved 72 units total: about a 109,000 kwh reduction per year; and at YAE, 9 units total: about a 9,400 kwh reduction per year. We will continue to work on achieving these reductions. As a result, the air conditioning load caused by a decline in thermal release from the equipment to the work area was reduced.
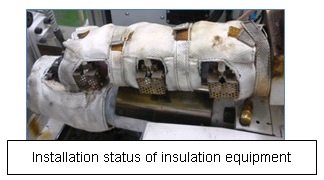
● Production system activities
YAE has reduced power consumption by 111,500 kwh/year by using vacuum pumps, which have been in place for some time, and has reduced air consumption (340,000 kwh/year) by revamping the method for extracting products from the molding machine.
● Energy conservation of plating tank (Akishima Plant)
We reduced heater electricity consumption by 2,566 kwh per year by installing insulating material on the pipe and tank sections of the plating line. As a result, the air conditioning load caused by thermal loss from the equipment to the work area was reduced.
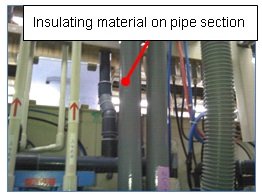
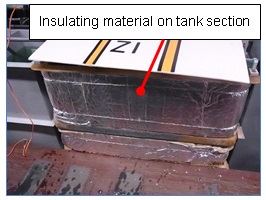
Energy conservation at plant facilities
● Air conditioning heat source refurbishment (third refurbishment of three-year plan from FY14-16 [within the Akishima Plant])
We upgraded to an air-cooled heat pump chiller (energy-saving device) due to facility upgrade (conventional turbo refrigeration unit and boiler) and attempted to save space in the turbo refrigeration unit cooling tower area and air conditioning machine room. As a result, the amount of supplementary water (about 1,700 m3/year before) for the cooling tower required thus far, was zero.
● Switching from mercury lighting to LED lighting (within the Akishima Plant)
In addition to saving energy, preparing for the 2020 discontinuation of the manufacture of specified mercury-added products, out of the total 115 lighting units at Akishima Plant, 43 units were upgraded between fiscal 2014 and 2016 and electricity consumption was reduced by 40,800 kwh. The remaining 72 units are scheduled to be systematically upgraded by fiscal 2019.
A mercury lighting unit
An LED lighting unit
We upgraded the building’s outer lighting from mercury lighting to LED lighting and reduced electric power consumption by 200 kwh per year.
LED lighting
We upgraded two substation transformers to top runner transformers and reduced consumption by 11,380 kwh per year.
● Reduced no-load loss of transformer by removing unnecessary substations (within the Akishima Plant)
Reduced by 72,000 kwh per year by removing unnecessary substations.
● Improved operation of clean room air conditioners (within the Akishima Plant)
We reduced consumption by about 92,244 kwh per year by adjusting operation mode (switching between temperature control and ventilation) while monitoring the cleanliness, temperature, and humidity of air conditioners in the No. 3 Plant’s lab.
● Utility-related activities
At YAE, we reduced electric power consumption by reducing cooling load (6,100 kWh/year) using a snow room, changing lighting to LED (7,800 kWh/year), improving heating efficiency by using waste heat (9,600 kWh/year), and adjusting the compressor's pressure setting (185,500 kwh/year)
● Adopting LED lighting in plants
We reduced electricity consumption at the FAE Plant by changing the lighting of the machine tool area, where operation times are long, to LED lighting and reduced consumption by 14,900 kwh/year on an annual cumulative basis.
● Equipment upgrade
n fiscal 2016, SAE expects a total energy-saving effect of about 97,000 kwh/year by upgrading to two energy-saving models of air conditioners (65,000 kwh/year)*, and changing 42 fluorescent lighting units in the machining building to LED lighting (32,000 kwh/year, the remaining 3 units have already been changed to LED).
*Efficient operation enabled by inverter control, unit control, etc.
Activities to increase awareness of measures to fight global warming
Introduced here are several fiscal 2016 efforts made to increase awareness of global warming measures.- Environment Month (June 1 to June 30)
Environment Month publicity and a wide range of Environment Month activities were held at each site.- Campaign to stop automotive idling
- No Driving Day
- Eco-driving training
- Clean up campaign around each work site, and other activities
- Environmental education concerning energy saving (July 8 through August 26)
All employees of the JAE Group in Japan took part in e-learning.
(For details, see the Environmental Education section) - Warm Biz and Cool Biz
- Cool Biz (May 9 through October 31)
- Warm Biz (November 1 through March 31)
- Participation in energy-saving “Lights Down” campaign (June 21 and July 7)
On summer solstice and “Tanabata” nights, for the two hours from 8 to 10 pm, called “Lights Down” time, as many lights as possible are switched off at each work site and workers do the same in their homes.
June 21: Summer solstice lights down (black illumination)
July 7: “Tanabata Lights Down” (Cool Earth Day)